Dry-type transformers are vital components in electrical systems, providing efficient voltage transformation without the use of oil for insulation. To ensure these transformers operate optimally and to detect any potential performance issues, it's essential to conduct thorough testing and troubleshooting procedures.
Visual Inspection
The testing process typically begins with a visual inspection of the
dry-type transformer. Look for signs of physical damage such as cracks, leaks, or overheating. Inspect the connections, terminals, and wiring for any loose connections or corrosion, as these issues can impact the transformer's performance and safety.
Insulation Resistance Test
Using a megohmmeter, perform an insulation resistance test on the transformer's windings. This test evaluates the integrity of the insulation between the windings and the transformer's core. Compare the measured insulation resistance values against the manufacturer's recommended values to identify any insulation problems that could lead to electrical faults or failures.
Transformer Turns Ratio (TTR) Test
Conduct a Transformer Turns Ratio (TTR) test to verify the turns ratio of the transformer's primary and secondary windings. This test ensures that the transformer is providing the correct voltage transformation. Compare the measured turns ratio with the rated turns ratio specified by the manufacturer to confirm proper operation.
Winding Resistance Test
Measure the resistance of the transformer windings using a low-resistance ohmmeter. This Winding Resistance Test helps identify any abnormalities or faults in the windings that could affect the transformer's performance. Compare the measured winding resistance values with the manufacturer's specifications to detect potential issues.
Voltage and Current Measurements
Connect a voltmeter and an ammeter to the primary and secondary circuits of the transformer. Measure the voltage and current under load conditions to verify that the transformer is operating within its rated voltage and current limits. Any deviations from these limits could indicate performance issues or overloading problems.
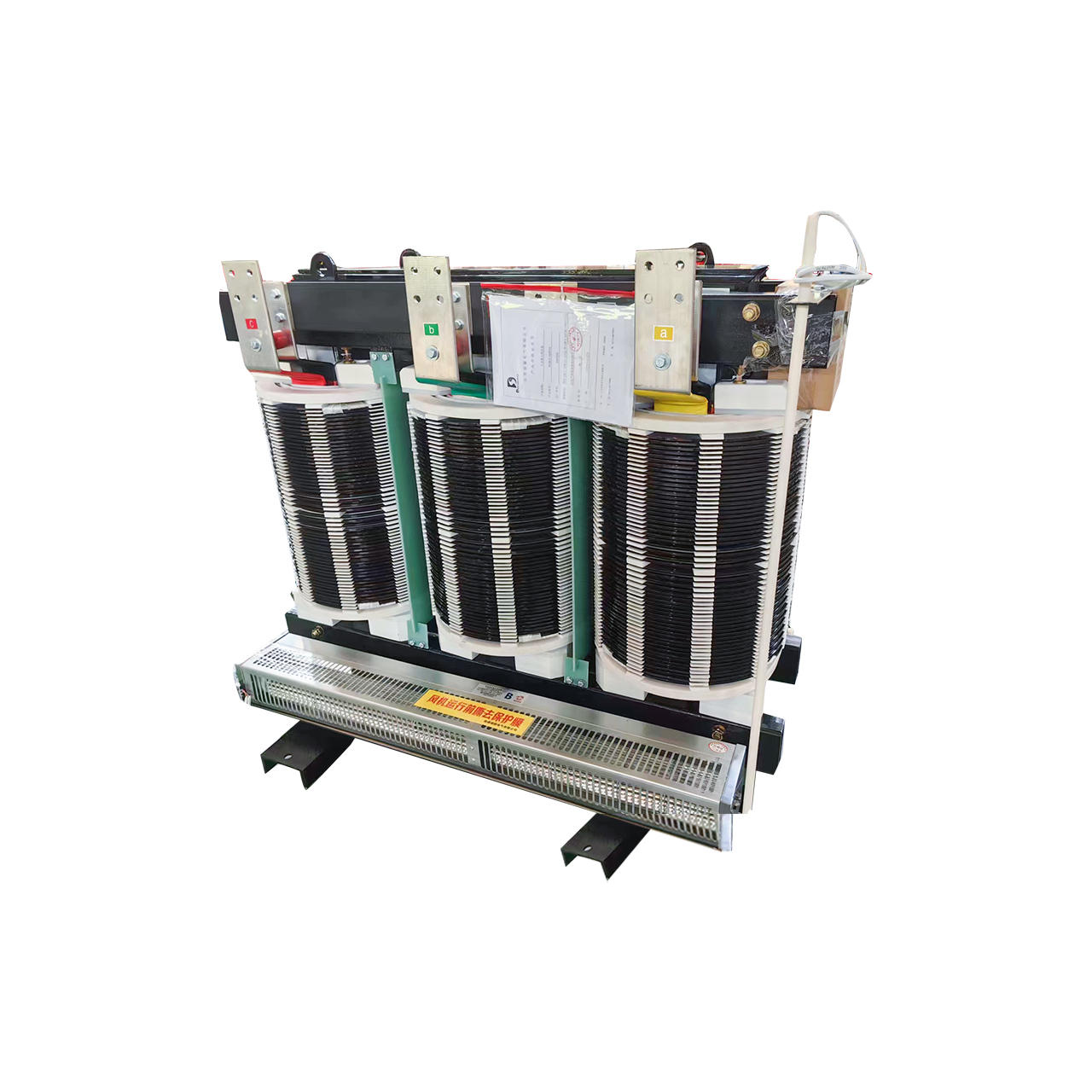
Temperature Measurements
Monitor the temperature of the
dry-type transformer's core and windings using temperature sensors or infrared thermometers. Ensure that the temperature remains within the specified limits during operation to prevent overheating, which can lead to insulation degradation and other issues. Excessive temperatures may indicate problems such as overloaded circuits or insufficient cooling.
Noise and Vibration Analysis
Listen for any unusual noise or vibrations emanating from the transformer during operation. Excessive noise or vibration could signify mechanical issues, loose components, or resonance problems that require further investigation. Addressing these issues promptly can prevent damage and ensure the transformer's longevity.
Short-Circuit and Overload Testing
Simulate short-circuit and overload conditions to evaluate the transformer's response and protective features. Verify that the transformer can withstand short-duration overloads and fault conditions without sustained damage. Testing these scenarios helps ensure the transformer's reliability and safety during real-world operating conditions.
Data Logging and Trend Analysis
Utilize data logging equipment to record voltage, current, temperature, and other relevant parameters over time. Analyze the data trends to identify any recurring issues or abnormalities that may require corrective action. Regular data logging and trend analysis can help detect performance degradation early and prevent potential failures.
Contact Us